A butterfly valve is a fluid control device. It uses a 1/4 turn rotation to control the flow of media in various processes. Knowing the materials and functions of the parts is vital. It helps to choose the right valve for a specific use. Each component, from the valve body to the valve stem, has a specific function. They are made of materials suitable for the application. They all play a vital role in ensuring efficient operation and maintenance. Proper understanding of these components can improve system performance and service life. Butterfly valves are used in many fields due to their versatility. Industries like water treatment, chemical processing, and food and beverage use these valves. Butterfly valves can handle different pressures and temperatures. So, they suit both high and low-demand environments. In addition, low cost and ease of installation make it stand out among many valves.
1. Butterfly Valve Part Name: Valve body
A butterfly valve's body is a shell. It supports the valve disc, seat, stem, and actuator. The butterfly valve body is used to connect to the pipeline to keep the valve in its place. Also, the valve body must withstand various pressures and conditions. So, its design is crucial to the performance.
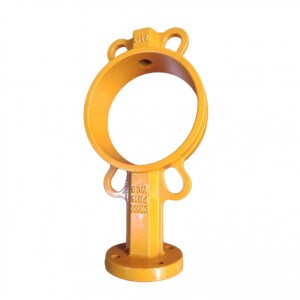

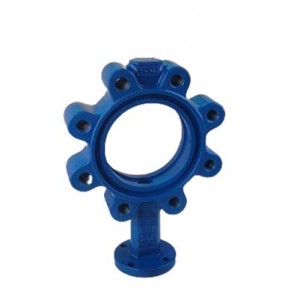
Valve body material
The valve body's material depends on the pipeline and media. It also depends on the environment.
The following are commonly used materials.
-Cast iron, the cheapest type of metal butterfly valve. It has good wear resistance.
-Ductile iron, compared with cast iron, has better strength, wear resistance and better ductility. So it is suitable for general industrial applications.
-Stainless steel, has great stability and corrosion resistance. It's better for corrosive fluids and sanitary uses.
-WCB, with its high hardness and strength, is suitable for high-pressure, high-temperature applications. And it is weldable.
2. Butterfly Valve Part Name: Valve disc
The butterfly valve disc is located in the center of the valve body and rotates to open or close the butterfly valve. The material is in direct contact with the fluid. So, it must be chosen based on the medium's properties. Common materials include sphere nickel plating, nylon, rubber, stainless steel, and aluminum bronze. The thin design of the valve disc can minimize flow resistance, thereby saving energy and improving the efficiency of the butterfly valve.


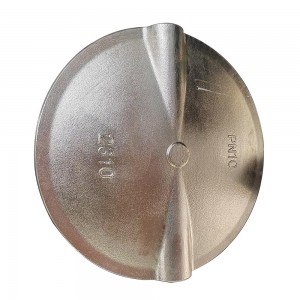

valve disc types.
Valve disc type: There are several types of valve discs for different applications.
-Concentric valve disc is aligned with the center of the valve body. It is simple and cost-effective.
-Double eccentric valve disc has a rubber strip embedded on the edge of the valve plate. It can improve the sealing performance.
The triple eccentric disc is metal. It seals better and wears less, so it's good for high-pressure environments.
3. Butterfly Valve Part Name: Stem
The stem connects the disc box actuator. It transmits the rotation and force needed to open or close the butterfly valve. This component plays a key role in the mechanical operation of the butterfly valve. The stem must withstand a lot of torque and stress during operation. So, the required material requirements are high.
The valve stem material
The stem is usually made of strong materials, like stainless steel and aluminum bronze.
-Stainless steel is strong and resistant to corrosion.
-Aluminum bronze resists it very well. They ensure long-term reliability.
-Other materials may include carbon steel or alloys. They are chosen for specific operating requirements.
4. Butterfly Valve Part Name: Seat
The seat in the butterfly valve forms a seal between the disc and the valve body. When the valve is closed, the disc squeezes the seat. This prevents leakage and keeps the pipeline system intact.
The butterfly valve seat must withstand a variety of pressures and temperatures. The choice of seat material depends on the specific application. Rubber, silicone, Teflon and other elastomers are common choices.




Valve seat types
There are several types of seats to meet various applications. The most common types are:
-Soft valve seats: Made of rubber or Teflon, they are flexible and resilient. These seats are ideal for low-pressure, normal-temperature applications that require tight shutoff.
-All metal valve seats: are made of metals, like stainless steel. They can withstand high temperatures and pressures. These valve seats are suitable for demanding environments that require durability.
-Multi-layer valve seats: Made of graphite and metal stacked at one time. They combine the characteristics of soft valve seats and metal valve seats. So, This multi-layer seat achieves a balance between flexibility and strength. These valve seats are for high-performance sealing applications. They can seal even when worn.
5. Actuator
The actuator is the mechanism that operates the butterfly valve. It turns the valve plate to open or close the flow. The actuator can be manual (handle or worm gear) or automatic (pneumatic, electric, or hydraulic).




Types and materials
-Handle: Made of steel or cast iron, suitable for butterfly valves of DN≤250.
-Worm gear: Suitable for butterfly valves of any caliber, labor-saving and low price. Gearboxes can provide a mechanical advantage. They make it easier to operate large or high-pressure valves.
- Pneumatic actuators: use compressed air to operate valves. They are usually made of aluminum or steel.
- Electric actuators: use electric motors and are installed in housings made of materials such as aluminum or stainless steel. There are integral and intelligent types. Waterproof and explosion-proof electric heads can also be selected for special environments.
Hydraulic actuators: use hydraulic oil to operate butterfly valves. Their parts are made of steel or other strong materials. It is divided into single-acting and double-acting pneumatic heads.
6. Bushings
Bushings support and reduce friction between moving parts, like valve stems and bodies. They ensure smooth operation.
Materials
- PTFE (Teflon): low friction and good chemical resistance.
- Bronze: high strength and good wear resistance.
7. Gaskets and O-rings
Gaskets and O-rings are sealing elements. They prevent leakage between valve components and between valves and pipelines.
Materials
- EPDM: commonly used in water and steam applications.
- NBR: suitable for oil and fuel applications.
- PTFE: High chemical resistance, used in aggressive chemical applications.
- Viton: Known for its resistance to high temperatures and aggressive chemicals.
8. Bolts
Bolts hold the butterfly valve's parts together. They ensure the valve is strong and leak-proof.
Materials
- Stainless steel: Preferred for its corrosion resistance and strength.
- Carbon steel: Used in less corrosive environments.
9. Pins
The pins connect the disc to the stem, allowing for smooth rotational motion.
Materials
- Stainless steel: Corrosion resistance and high strength.
- Bronze: Wear resistance and good machinability.
10. Ribs
The ribs provide additional structural support to the disc. They can prevent deformation under pressure.
Materials
- Steel: High strength and stiffness.
- Aluminum: Suitable for lightweight applications.
11. Linings and coatings
Liners and coatings protect the valve body and parts from corrosion, erosion, and wear.
- Rubber linings: Such as EPDM, NBR, or neoprene, used in corrosive or abrasive applications.
- PTFE coating: chemical resistance and low friction.
12. Position indicators
The position indicator shows the open or closed state of the valve. This helps remote or automated systems monitor the valve position.
Types
- Mechanical: a simple mechanical indicator attached to the valve stem or actuator.
- Electrical: a sensor